About the new-energy vehicle
New energy vehicles refer to the use of unconventional vehicle fuel as a power source, integrated vehicle power control and drive advanced technology, the formation of advanced technical principles, with new technology, new structure of the car.
New energy vehicles include four types of hybrid electric vehicles and pure electric vehicles
Fuel cell electric vehicles, other new energy sources such as supercapacitors, flywheels and other efficient energy storage vehicles.
Unconventional vehicle fuels refer to fuels other than gasoline, diesel, natural gas, liquefied petroleum gas, ethanol gasoline, methanol, and DME.
New energy vehicles have the advantages of little pollution and environmental protection.
Pure electric vehicles can achieve zero pollution during operation and do not emit harmful gases that pollute the atmosphere at all.
Even when converted into emissions from power plants, they pollute less than conventional cars because power plants have a higher energy conversion rate.
New energy vehicles also have the characteristics of less noise and more comfortable, and the noise and vibration levels of the motor in operation are far less than that of the traditional internal combustion engine.
At idle and low speeds, the comfort of electric cars is much higher than that of conventional cars.
New-energy vehicle Leaf Spring Characteristics
1. The Mitsubishi Leaf Spring MB10F-FL acts as a linkage for holding the axle in position and thus separate linkages are not necessary. It makes the construction of the suspension simple and strong.
2. Because the positioning of the axle is carried out by the leaf springs, it is disadvantageous to use soft springs i.e. springs with low spring constant.
3. Therefore, this type of suspension does not provide good riding comfort. The inter-leaf friction between the leaf springs affects the riding comfort.
4. Acceleration and braking torque cause wind-up and vibration. Also wind-up causes rear-end squat and nose-diving.
5. The inter-leaf friction damps the spring's motion and reduces rebound, which until shock absorbers were widely adopted was a great advantage over helical springs.
ISO Certification
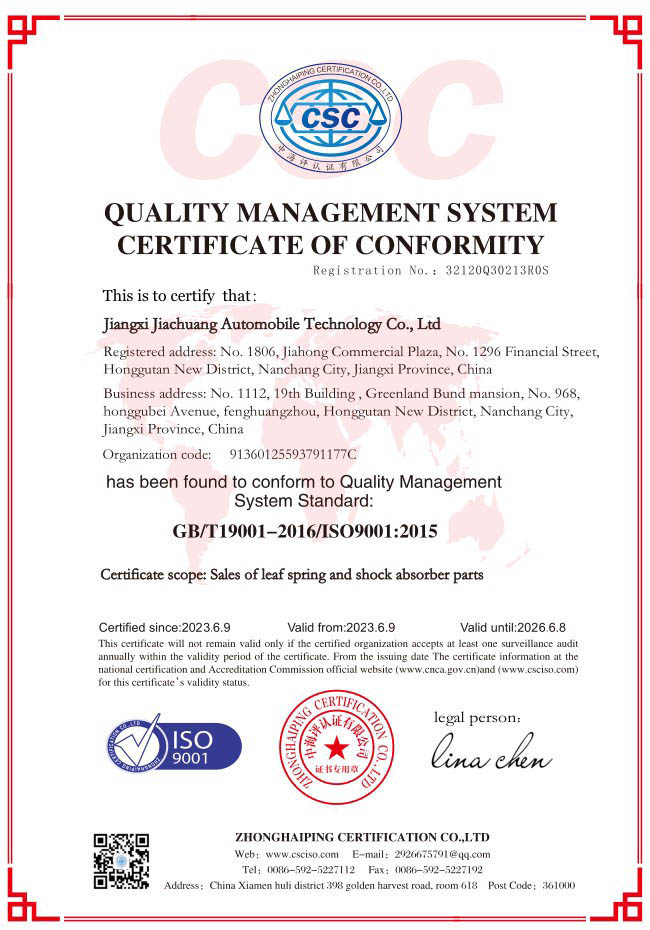
Key Points Keep The High Quality
1) Raw material . |
Thickness less than 20mm. we choose SUP9/55Cr3/SAE5160H as the product material |
Thickness from 20-30mm. wE choose SUP11A/50CrVA |
Thickness more than 30mm. We choose 51CrV4 as the raw material |
Thickness more than 50mm. We choose 52CrMoV4 as the raw material |
2) Quchenging Process |
We strickly controled the steel temeprure around 800 degree. |
we swing the spring in the qenching oil among 10 seconds according to the spring thickness. |
3)Shot Peening. |
Each assmembing spring set under stress peening . |
Fatigue test can reach over 150000 cycus |
4) Painting |
Each leaf under cataphoresis painting. |
Salt spray testing reach 500hours |
Production Process
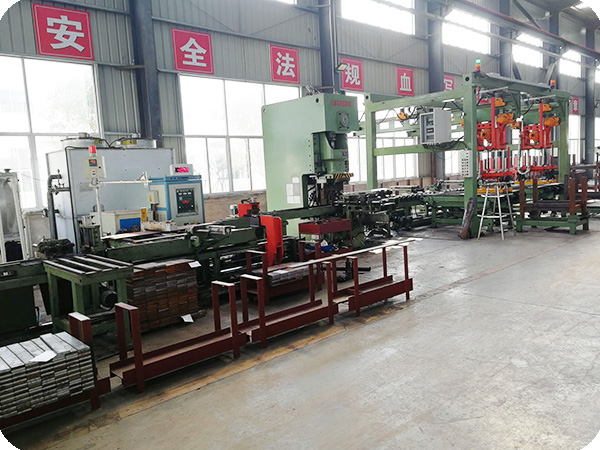
1.Material Cutting
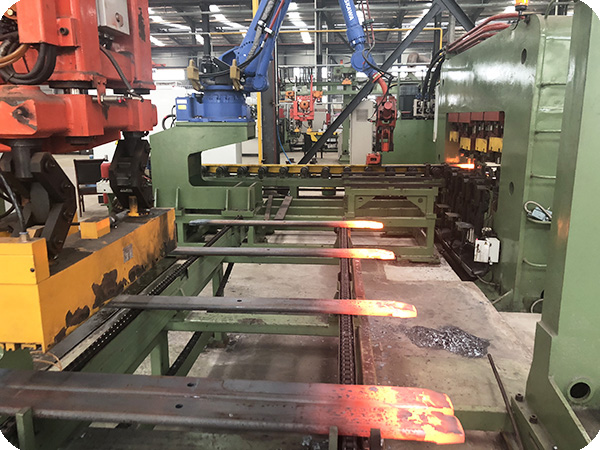
4.Edge Cutting
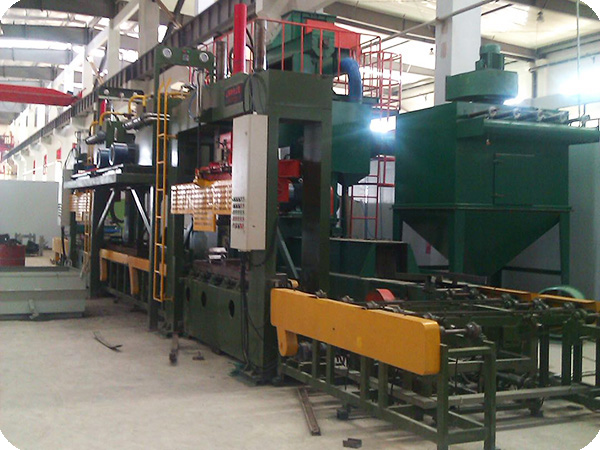
7.Stress Peening
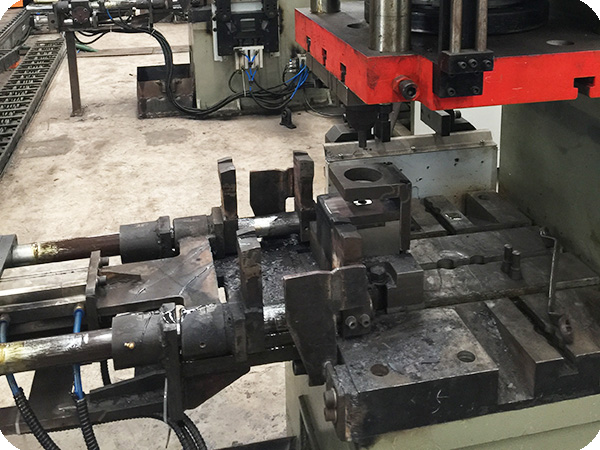
2.Punching
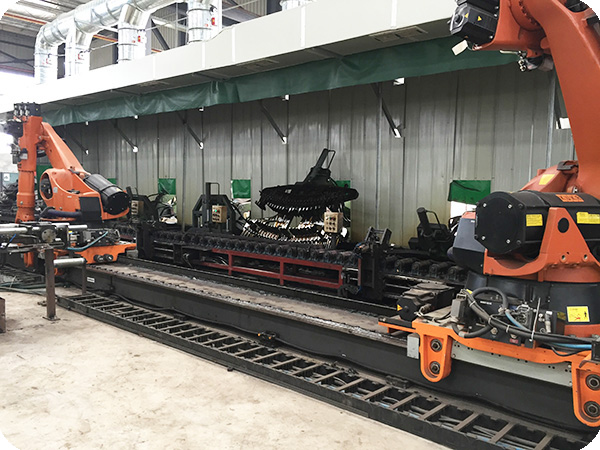
5.Quenching
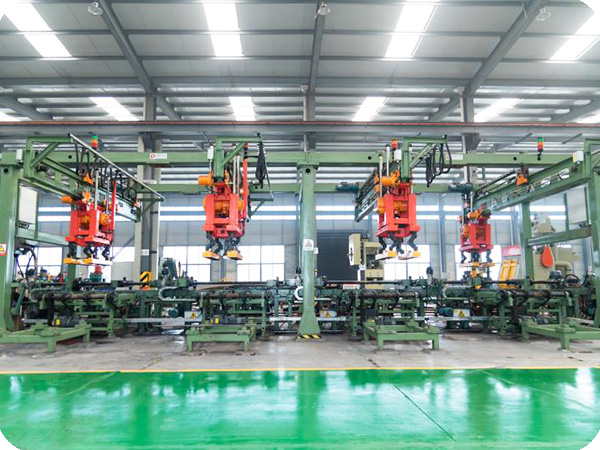
8.Assembling
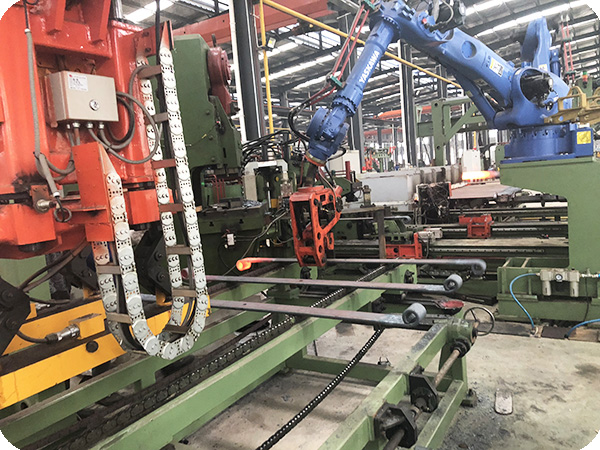
3.Eye Rolling

6.Tempering
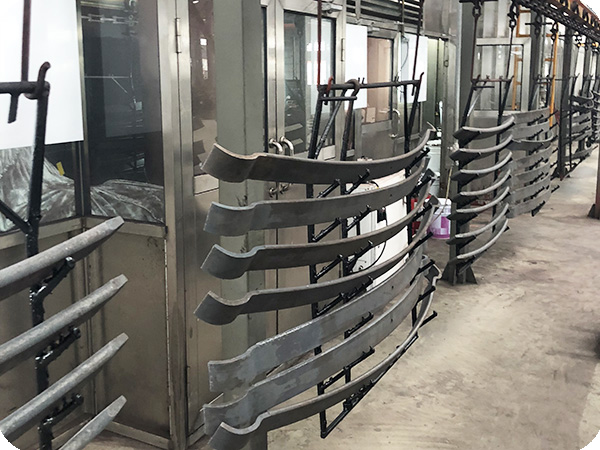
9.Painting
FAQ
Q1: What type of leaf spring could you produce ?
A: We can produce most kinds of springs in the market. especially on the parabolic springs.
Q2: What material could you supply for leaf spring?
A: Our material grade should be SUP9/SUP9A /SUP11A/51CrV4 /52CrMoV4/ even 55Cr3 and SAE5160H as well .
Q3: How long will be your delivery time?
A: 20-40days. If material stock enough around 20days. if not,would be 40days
Q4: What payment terms are acceptable?
A: TT and LC at sight
Q5: What is the packing?
A: No fumigation wooden pallet . we also can pack according to whatever you request if reasonable.
Q6:How about the surface finishing ?
A : electrophoresis coating (black,red,gray,or as customer’s requests )
-
Hot Sale Leaf Spring For Trailer 90*9/13 Americ...
-
ZL7808-A Parabolic Rear Leaf Spring for Vehicle...
-
High quality TRA-2726 SUP9 steel leaf spring fo...
-
Hot selling 11436 trailer suspension part leaf ...
-
UNIVERSAL 70-13(5) D12 Trailer Truck Bogie Spri...
-
JMC02F/6 Parabolic Rear Leaf Spring for Vehicle...